Understanding LVL Construction: A Comprehensive Guide
Understanding LVL Construction: A Comprehensive Guide
LVL construction, or Laminated Veneer Lumber construction, is a popular technique in the building industry known for its strength, durability, and versatility. In this comprehensive guide, we will delve into what LVL construction entails, explore its benefits, understand the process involved, and compare it to traditional construction methods.
What is LVL Construction?
LVL construction is a type of engineered wood construction that utilizes multiple layers of veneer to create strong and durable structural members. But let’s dive deeper into the fascinating world of LVL construction and explore its definition, basic principles, and key components.
Definition and Basic Principles
LVL stands for Laminated Veneer Lumber, which is made by fusing together several layers of thin veneer sheets with an adhesive. These veneers are typically made from low-grade or fast-growing timber, making LVL construction an eco-friendly alternative to solid wood construction. This not only reduces the demand for high-quality timber but also maximizes the utilization of sustainable wood resources.
The basic principle behind LVL construction is that by layering the veneer sheets in alternating grain directions, the resulting lumber becomes significantly stronger and more resistant to warping or twisting. This ingenious technique harnesses the natural strength of wood fibers and distributes the forces evenly throughout the LVL member. As a result, LVL construction offers exceptional dimensional stability and load-bearing capacity, making it a preferred choice for architects, engineers, and builders.
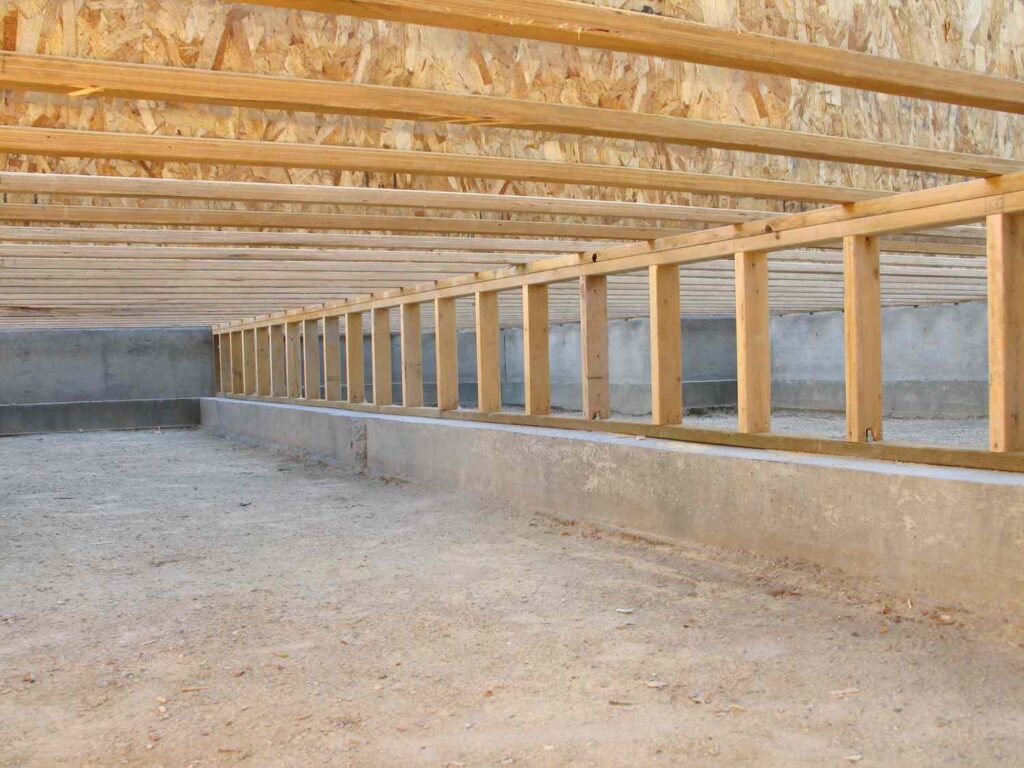
Key Components of LVL Construction
Now that we understand the fundamental principles of LVL construction, let’s explore the key components that make it all possible:
- Laminated Veneer Lumber (LVL) beams: These beams are the backbone of LVL construction. LVL beams are typically manufactured in various sizes and lengths, allowing for flexible design and construction options. Whether it’s a residential, commercial, or industrial project, LVL beams provide the necessary strength and stability to support heavy loads and span long distances.
- Adhesive: The adhesive used in LVL construction is a crucial element that binds the veneers together. High-quality adhesives ensure strong bond strength and long-lasting performance. These adhesives are specifically formulated to withstand the rigors of construction, including exposure to moisture, temperature fluctuations, and other environmental factors. The result is a robust and durable LVL member that can withstand the test of time.
- Supporting hardware: In some cases, LVL construction may require additional components such as connectors, brackets, or metal plates to enhance structural integrity and join different elements together. These supporting hardware elements are carefully selected and engineered to complement the strength and characteristics of LVL members, ensuring a seamless integration and optimal performance.
By combining these key components, LVL construction offers a versatile and reliable solution for a wide range of construction projects. From residential homes to commercial buildings and even bridges, LVL construction continues to revolutionize the industry with its exceptional strength, sustainability, and design flexibility.
The Benefits of LVL Construction
Strength and Durability
One of the primary advantages of LVL construction is its exceptional strength and durability. The layering and bonding process used in manufacturing LVL beams results in a material that can withstand heavy loads and resist bending, warping, or twisting over time.
LVL construction is also highly resistant to moisture, insects, and rot, making it an ideal choice for applications in humid or damp environments.
Furthermore, the manufacturing process of LVL beams involves precise control over the quality and orientation of each layer, ensuring consistent strength and performance across the entire beam. This attention to detail enhances the structural integrity of LVL construction, providing long-lasting support for various building projects.
Versatility in Design
Another significant benefit of LVL construction is its versatility in design. LVL beams can be manufactured in various sizes and lengths, allowing architects and builders greater flexibility in creating unique and complex structures. Read more about versatility on https://versatileeducaare.com/
With LVL construction, it is possible to achieve long spans, open floor plans, and innovative architectural designs that may not be feasible with traditional construction methods.
In addition to its structural versatility, LVL construction offers aesthetic flexibility as well. The smooth and uniform surface of LVL beams provides a clean and modern look that can enhance the visual appeal of both residential and commercial spaces. This aesthetic quality, combined with the structural capabilities of LVL construction, makes it a popular choice among designers and builders seeking both form and function in their projects.
Environmental Impact
LVL construction is considered an environmentally friendly choice due to several factors. Firstly, the manufacturing process of LVL beams utilizes low-grade or fast-growing timber, reducing the demand for high-quality hardwood.
Additionally, LVL construction helps minimize waste by utilizing timber veneers that would otherwise be discarded. The adhesive used in LVL construction is also typically low in VOC (volatile organic compounds), ensuring a reduced environmental impact.
Furthermore, the longevity and durability of LVL construction contribute to sustainable building practices by reducing the need for frequent replacements or repairs. This extended lifespan not only conserves resources but also minimizes the overall environmental footprint of construction projects utilizing LVL beams.
The Process of LVL Construction
Material Selection and Preparation
The first step in LVL construction is selecting and preparing the materials. The veneer sheets used in LVL beams are carefully chosen for their quality and structural integrity. Manufacturers often source these veneer sheets from sustainably managed forests to ensure environmental responsibility. The sheets are then trimmed to the desired dimensions with precision equipment, guaranteeing uniformity in size and shape. Each veneer sheet is meticulously inspected for any defects or imperfections that could compromise the final product, ensuring only the highest quality materials are used in the construction process.
Once the veneer sheets are ready, they undergo a meticulous drying process to reduce moisture content and ensure stability. This step is crucial in preventing warping or twisting of the finished LVL beams. The drying process may involve kiln-drying or air-drying, depending on the specific requirements of the manufacturer. Properly dried veneer sheets provide the foundation for durable and reliable LVL beams that can withstand the test of time.
Assembly and Installation
After material preparation, the veneer sheets are layered together with adhesive in between each sheet. The type of adhesive used is carefully selected to ensure optimal bonding strength and durability. These layers are then pressed and bonded under high pressure in a specialized press machine. The combination of pressure and heat activates the adhesive, creating a solid and cohesive LVL beam that exhibits exceptional strength and dimensional stability. Click here to read more about pressure.
The finished LVL beams can be installed in various ways, depending on the specific construction requirements. They can be used as floor joists to support the weight of a structure, roof beams to provide structural integrity to the roof system, headers for door and window openings, or support columns for vertical load-bearing applications. The versatility of LVL beams makes them a popular choice in a wide range of construction projects, from residential homes to commercial buildings.
Finishing and Maintenance
Once the LVL beams are installed, they can be finished with paint, stain, or other coatings to enhance their aesthetics and protect them from the elements. The finishing not only adds visual appeal to the structural elements but also acts as a protective layer against moisture, UV rays, and other environmental factors. Regular maintenance, such as inspections for signs of damage or wear, is recommended to ensure the long-term performance of LVL construction. Timely repairs and maintenance can prolong the lifespan of LVL beams and contribute to the overall durability of the structure.
LVL Construction vs Traditional Construction
Cost Comparison
While upfront costs may vary depending on the specific project requirements, LVL construction can often be a cost-effective alternative to traditional construction methods.
The versatility and strength of LVL beams can often reduce the need for additional structural elements, resulting in potential cost savings. Additionally, the efficiency of the manufacturing process and the availability of low-grade timber contribute to the overall affordability of LVL construction.
When it comes to cost, it’s important to consider not only the initial investment but also the long-term savings. LVL construction is known for its durability and resistance to warping, shrinking, and splitting. This means that maintenance costs over the lifespan of a building constructed with LVL can be significantly lower compared to traditional construction methods.
Read more on: Best LVL Beam Suppliers
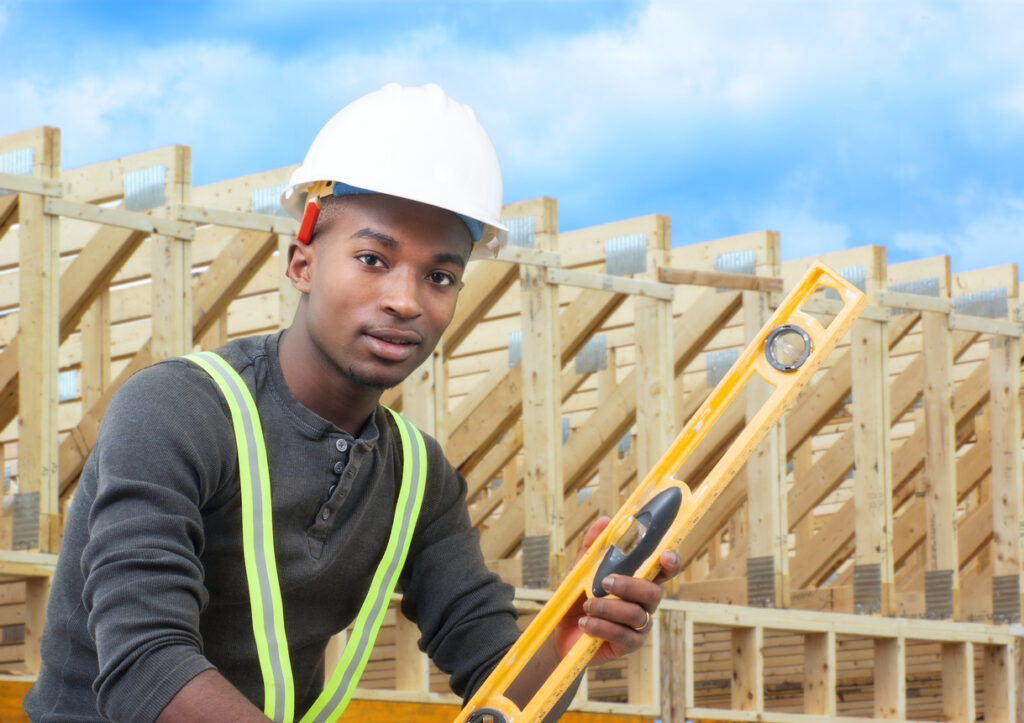
Time Efficiency
LVL construction can significantly expedite the construction process due to its prefabricated nature. LVL beams can be manufactured off-site and delivered to the construction site ready for installation. This reduces on-site labor time, allowing for faster project completion.
Furthermore, the dimensional stability of LVL beams eliminates the need for lengthy drying times typically associated with traditional solid wood construction materials. This means that construction projects can proceed without delays caused by waiting for materials to acclimate to the environment.
Time is money in the construction industry, and LVL construction offers a time-efficient solution that can help meet tight deadlines and reduce overall project duration.
Sustainability Factors
From an environmental perspective, LVL construction offers several sustainability advantages compared to traditional construction methods. By utilizing low-grade or fast-growing timber, LVL construction reduces the demand for high-quality hardwood, helping to preserve forests and promote responsible forestry practices.
Additionally, the bonding process used in LVL construction enhances the overall structural performance, allowing for the use of smaller, more sustainable timber pieces rather than large solid wood beams. This not only reduces waste but also maximizes the utilization of available resources.
Furthermore, LVL construction can contribute to energy efficiency in buildings. The insulation properties of LVL beams can help reduce heat transfer, resulting in lower energy consumption for heating and cooling.
By choosing LVL construction, builders and homeowners can make a positive impact on the environment while still enjoying the benefits of a strong and reliable construction method.
In conclusion, LVL construction is a versatile and sustainable construction technique that offers numerous benefits over traditional methods. With its exceptional strength, durability, and design flexibility, LVL construction has become an increasingly popular choice for architects, builders, and homeowners alike.